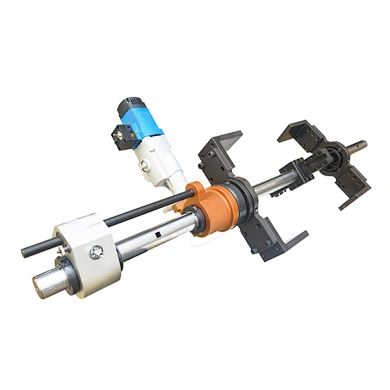
# Portable Flange Facing Machine: Essential Tool for On-Site Machining
## Introduction to Portable Flange Facing Machines
In the world of industrial maintenance and repair, portable flange facing machines have become indispensable tools for on-site machining operations. These compact yet powerful devices enable technicians to perform precision machining tasks directly at the job site, eliminating the need to remove large components or transport them to a workshop.
## Key Features of Modern Portable Flange Facing Machines
Today’s portable flange facing machines offer a range of advanced features that make them highly efficient and versatile:
– Compact and lightweight design for easy transportation
– Powerful cutting capabilities for various flange materials
– Precision machining with high accuracy tolerances
– Adjustable configurations for different flange sizes
– User-friendly operation with minimal setup time
## Applications Across Industries
Portable flange facing machines find applications in numerous industries where flange maintenance is critical:
### Oil and Gas Industry
In pipeline systems and refineries, these machines ensure proper flange sealing surfaces for leak-proof connections.
### Power Generation
Power plants rely on portable flange facers to maintain turbine and boiler connections during scheduled maintenance.
### Shipbuilding and Repair
Marine applications benefit from on-site flange machining for propulsion systems and piping networks.
### Chemical Processing
Chemical plants use these machines to maintain flange integrity in corrosive environments.
## Advantages Over Traditional Methods
The use of portable flange facing machines offers significant benefits compared to conventional approaches:
– Reduced downtime by eliminating component removal
– Cost savings from avoiding transportation of large parts
– Improved safety by minimizing handling of heavy components
– Higher precision results compared to manual methods
– Flexibility to work in confined or remote locations
## Choosing the Right Portable Flange Facing Machine
When selecting a portable flange facing machine, consider these important factors:
– Maximum and minimum flange diameter capacity
– Power source requirements (electric, hydraulic, or pneumatic)
– Material compatibility and cutting capabilities
– Portability features and weight
– Available accessories and tooling options
– Manufacturer support and service availability
## Maintenance and Care Tips
To ensure optimal performance and longevity of your portable flange facing machine:
– Regularly clean and lubricate moving parts
– Inspect cutting tools for wear and replace as needed
– Store the machine in a dry, protected environment
– Follow manufacturer’s guidelines for maintenance intervals
– Train operators on proper usage techniques
## Future Trends in Portable Flange Facing Technology
The portable flange facing machine market continues to evolve with emerging technologies:
Keyword: portable flange facing machine
– Integration with digital measurement systems
– Advanced materials for lighter yet stronger constructions
– Improved automation features for enhanced precision
– Wireless connectivity for data logging and remote monitoring
– Environmentally friendly designs with reduced energy consumption
## Conclusion
Portable flange facing machines have revolutionized on-site machining operations across multiple industries. Their ability to deliver precision results in challenging environments makes them essential tools for maintenance teams worldwide. As technology advances, these machines will continue to play a vital role in ensuring the integrity and reliability of flange connections in critical industrial applications.